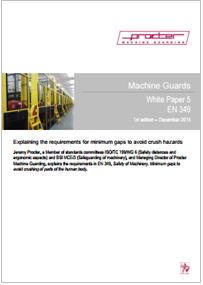
EN 349 White Paper Machine Guards
EN 349 Safety of machinery.
Minimum gaps to avoid crushing of parts of the human body (and BS EN 349 as published by BSI in the UK) has been with us since 1993 and has proven to be a very useful standard for machine builders and engineers designing or specifying guards, particularly perimeter guarding.
At the time of writing, the current version of the standard is BS EN 349:1993+A1:2008, with the 2008 amendment just adding a pair of appendices referencing the old and new Machinery Directives. EN 349 is Harmonised to the Machinery Directive 2006/42/EC and provides a presumption of conformity with certain essential health and safety requirements (EHSRs).
Compared with some other machinery safety standards, EN 349 is uncontroversial, simple to understand and straightforward to use, though care has to be taken in its application.
Risk assessment Before reaching for a copy of EN 349 and designing or specifying machine guards it is important to conduct a risk assessment, ideally in line with the requirements of EN ISO 12100:2010 Safety of machinery.
General principles for design. Risk assessment and risk reduction (with the equivalent in the UK being BS EN ISO 12100:2010).
If possible, the machine should be designed to be inherently safe so that it does not need measures such as guarding.
In fact EN 349 can help in this respect because if gaps are sufficiently large, then they do not need to be guarded to prevent crush injuries.
Nevertheless, a risk assessment should be the first step taken.
An EN ISO 12100:2010 risk assessment should cover all aspects of the machine’s lifecycle, including assembly, maintenance, disassembly and so on.
Although it may not seem obvious when reading EN 349, there is an implication that needs to be considered: it is easy to imagine situations where fingers could be crushed while handling heavy components during assembly, maintenance and disassembly.
Although the formal risk assessment may show the likelihood of occurrence to be small, the severity of the injury (finger amputation) is serious enough that the designer should take reasonably practicable steps to eliminate the risk.
In reality, it would be impossible to design-out all potential finger-crushing gaps, so there will be residual risks for which the appropriate action could be to state in the machine instructions that care must be taken when handling heavy parts (using appropriate lifting equipment if necessary) so as to avoid fingers being crushed.
The risk assessment also needs to take into account the people who are likely to be using the machinery because the anthropomorphic data used to determine the ‘safe’ gaps stated in EN 349 will not cover 100 per cent of the population or those wearing bulky clothing or PPE (personal protective equipment). Furthermore, EN 349 refers to children (if they are in the ‘population at risk’) whereas EN ISO 13857, relating to safety distances (see Normative references below), applies only to people of 14 years and older for upper and lower limbs, and children older than three years where the designer needs to address reaching through openings.
Explaining the requirements for minimum gaps to avoid crush hazards Jeremy Procter, a Member of standards committees ISO/TC 199/WG 6 (Safety distances and ergonomic aspects) and BSI MCE/3 (Safeguarding of machinery), and Managing Director of Procter Machine Guarding, explains the requirements in EN 349, Safety of Machinery.
Minimum gaps to avoid crushing of parts of the human body.
Procter
1st edition - December 2015